Organic Greenhouse Vegetable Production
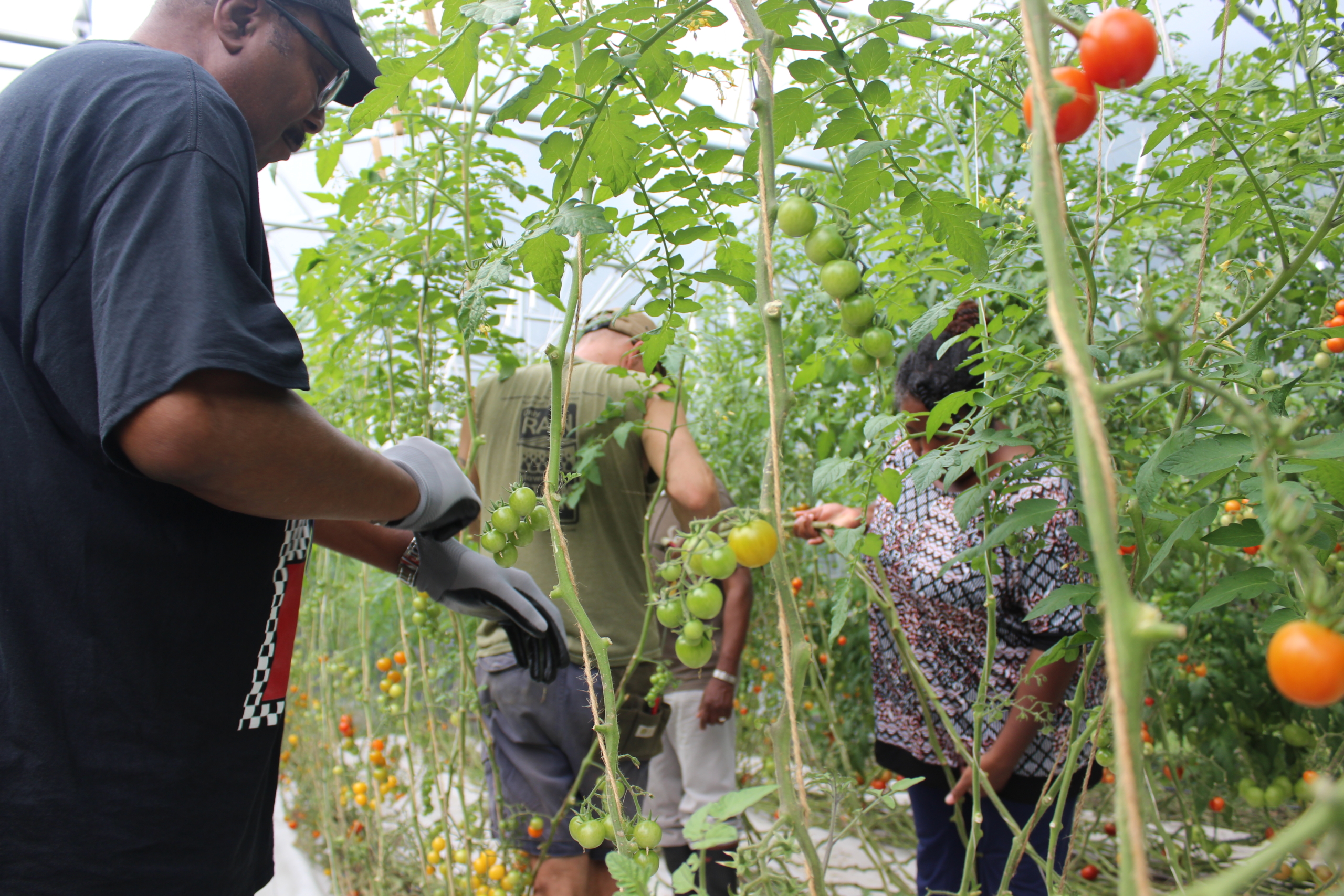
Photo: NCAT
By Lane Greer and Steve Diver, NCAT Agriculture Specialists
Updated by Tammy Howard and Chris Lent, with contributions from Ann Baier, Dan Birnstihl, and Daniel Prial
Abstract
Organic greenhouse vegetable production requires extensive upfront investment but can yield premium prices if the grower can identify a marketing channel without a lot of competition. The key to profitable greenhouse vegetable production is keeping annual costs low. The highest costs for greenhouse production are energy and labor. This publication includes information on energy conservation, organic fertility, and pest management, as well as resources on determining costs and revenues for growing organic greenhouse vegetables. This information—and resources on these topics—will enable growers to make decisions about the viability of this enterprise.
Contents
Introduction
An Overview of the Greenhouse Vegetable Industry
Market Evaluation
Greenhouse Energy Considerations
Organic Certification
Fertility and Soil Management
Weed Management
Pest Management
Greenhouse Systems
Economics of Greenhouse Production
Developments in the Greenhouse Industry
Conclusion
References
Further Resources
Introduction
This publication presents an overview of greenhouse production systems and profiles of farmers raising organic vegetables in greenhouses. This guide will give new growers ideas of how to set up their systems and provide more experienced farmers with examples of alternative methods of production and organic certification requirements unique to greenhouses.
Another ATTRA publication, Season Extension Techniques for Market Gardeners, contains further information on protected-shelter structures such as cold frames, high tunnels or hoophouses, and low tunnels.
Note: This publication touches on organic hydroponic production. With the National Organic Standards Board’s 2022 decision to allow hydroponic operations to become certified organic, the technology and information is still quite new and evolving. We will continue to follow and update this issue. We know and acknowledge that the debate over certifying hydroponics is still quite contentious, but we feel that it is important to include all greenhouse information that is certifiable through the National Organic Program standards.
An Overview of the Greenhouse Vegetable Industry
In 2017 in North America, there were nearly 15,000 acres of “food crops grown under protection,” which includes hoophouses and other structures, as well as greenhouse production, according to the USDA’s U.S. Census of Agriculture. Of this total, 2,990 acres were in the United States, 3,608 acres were in Canada, and 9,084 acres were in Mexico (Burfield, 2019). Mexico has been the largest supplier to the North American market, possessing about 60% of production area. Remarkably, Mexican production area has exponentially increased in the past five years, to 57,000 acres in 2019 (Burfield, 2019). This increased protective culture came with a corresponding reduction in field-grown produce in Mexico. The United States receives 96% of Mexico’s greenhouse vegetable production, and the rest goes to Canada, claims Alfredo Diaz Belmontes, the director general of the Mexican Association of Protected Horticulture (Belmontes, 2016).
According to USDA’s Economic Research Service 2019 Organic Survey, there were 715 acres in organic greenhouse vegetable and mushroom production. (USDA ERS, 2019). Tomatoes are the leading organic greenhouse vegetable crop, with 152 acres in production, followed by European cucumbers, herbs, lettuce, peppers, and strawberries. The leading states in organic greenhouse tomato production are California, Pennsylvania, and Colorado, respectively. There are more than 700 types of organic vegetables grown in greenhouses in the United States, including tomatoes, mushrooms, and other vegetables and herbs (USDA ERS, 2019). The leading states in organic greenhouse vegetable production—other than tomatoes—are California and Pennsylvania (USDA ERS, 2019). Centers of greenhouse production are located in California, Arizona, and Colorado. These locations offer market competition, but they also provide a source of technical assistance, greenhouse supplies, and consulting.
Hoophouses vs. Greenhouses: What’s the difference?
The term “greenhouse” means different things to different people. With hoophouses (also referred to as high tunnels) and season-extension techniques further confusing the definition, it is important to distinguish between hoophouses and greenhouses. A greenhouse is typically used for year-round production with supplemental heating and cooling. It is a permanent structure and most zoning departments will require an inspection as such. Hoophouses, on the other hand, are considered non-permanent structures and are used for one to three seasons, depending on the climate. Greenhouse structures can be constructed with multiple types of materials, such as twin-wall polycarbonate, glass (rarely used anymore), and double-layer plastic. Hoophouses are not considered permanent structures even though they typically have concrete footings. Hoophouses minimize installation time, often exchanging the durability and overall strength of a standard greenhouse for the immediate benefits of a simpler design. They typically have one layer of poly plastic, roll-up sides for cooling and air flow, and often no electricity or environmental controls. Greenhouses tend to cost more to build, in part because their temperatures are maintained through heating and cooling systems. Because of the high cost of building and maintenance for either system, both greenhouses and hoophouses are best suited for high-value crops such as tomatoes, peppers, and cucumbers, as well as herbs and bedding plants.
Greenhouse and Hoophouse Grower’s Handbook, a new book by the editor of Growing for Market, goes into more depth on the topics discussed in this publication. See the Further Resources section for more information.
Market Evaluation
With so much competition from Canada and Mexico, it is important to evaluate your markets for a niche that is profitable. Small-scale growers who plan on direct marketing should carefully assess markets in a region that may already be saturated with hydroponic and hoophouse-grown produce. Organic and locally grown produce is a niche, but it will be important to differentiate your vegetables from the myriad of local, organic, hoophouse products that are sold through direct marketing channels, such as farmers markets and community supported agriculture. Other greenhouse niches include heirloom products, fresh herbs that cannot be shipped nationally, organic, and niche products.
A good example can be illustrated with the salad greens industry. Twenty years ago, mixed leaf lettuce was almost impossible to find. The undersupply led to extremely high prices; as much as $16 per pound was not uncommon. More and more small growers began producing salad greens, but it wasn’t until large growers entered the market that the price per pound went down significantly (to $6 to $10 a pound). Many growers can still get $4 to $6 a pound for greens, but large growers in California and Mexico have caused the price to stay low.
Intermediate marketing channels can be a good approach for smaller-scale or beginning greenhouse growers. Intermediate markets help retain your farm identity but allow for larger-scale and simplified production strategies compared to direct markets. Examples of intermediate markets are independent grocery stores, restaurants, food hubs or aggregators, and institutions. For more information on identifying and focusing on intermediate markets, see ATTRA’s Intermediated Markets tutorial.
Year-round production is key to maintaining a profitable greenhouse. However, this does not necessarily mean that growers should be producing the same crop year-round. (Winter tomatoes bring more money than do summer ones.) Another option would be to raise a crop other than vegetables, like bedding plants and transplants for early spring sales, or poinsettias for Christmas.
Another consideration for a profitable return with greenhouse vegetables is keeping costs down. Labor and energy are usually the two greatest greenhouse expenses. If you can find a way to decrease costs of either or both of these, your chances of making a profit will be strengthened.
Greenhouse Energy Considerations
Typically, combined utility and fuel costs are the third-highest expense for horticultural growers in the United States (USDA NASS, 2019). Because heating and cooling greenhouses accounts for a large portion of utility and fuel usage, understanding different types of greenhouse heating and cooling systems and how they function is important. In this section, we will review how most conventional greenhouses are heated and cooled and the fuels that are used for these purposes. We are only covering the typical or traditional greenhouse crop production systems for this section, not hydroponics and vertical greenhouse production systems. We also cover how to reduce these energy inputs with proven conservation measures that can be incorporated into the design of new greenhouses or, in most cases, retrofitted to existing greenhouses. Finally, we’ll cover some of the alternative heating and cooling systems and fuels that growers are using to reduce the use of fossil fuels.
Heating Systems
The most common type of heating equipment used in commercial greenhouses is forced hot air units. These are furnaces that blow air through a flame-heated heat exchanger and into the greenhouse space. They are often chosen because they are relatively inexpensive, can be sized easily to the amount of heated space, and are simple to install. If an operation expands, more units can be installed to heat additional space. Heat from these can also easily be ducted to heat the space under tables for tabletop production.
There are five types of direct-fired hot air units: gravity vented, power vented, separated combustion, high-efficiency condensing, and unvented. High-efficiency condensing units cost more but have more than 10% higher efficiency over other types of units (Sanford, 2011a). “Efficiency” here refers to how much heat is produced per unit of fuel used. Gas-fired units can achieve a 90%+ efficiency, while oil-fired units have a maximum efficiency of 85%. Unvented heaters utilize all the heat the unit produces to heat the greenhouse but also emit moisture and carbon dioxide (CO2) into the greenhouse interior. Some CO2 can be utilized by the plants, but too much can be detrimental to plant and human health, so unvented heaters should not be considered for greenhouse heating.
Hydronic heating systems are less commonly used. They rely on boilers to heat water for radiant heating of tabletops and in-ground root-zone heating systems. Some systems also use hot water for radiant heating of the air space in the greenhouse. Whichever type of heating system is used, investing in high-efficiency heating units (90% and higher thermal efficiency rating) can have an ROI of less than four years.
Infrared heating is common in greenhouse production where the plants are a uniform height. Infrared systems create infrared radiation that is transferred to plants and other objects in the greenhouse to heat them instantly. Only what needs to be heated—the plants—is heated and not the rest of the air in the greenhouse. For this reason, these systems can be energy efficient and economical. Usually, low-intensity infrared units are used for this application and are powered either by electricity or gas.
Heating Fuels
The most common fuels used in greenhouse heating equipment are natural gas, liquid propane gas (LPG), and No. 2 fuel oil. Heating systems that burn these fuels vary greatly, and the efficiency of a greenhouse heating system can depend not only on the heating equipment but on the type of fuel being used. For that reason, and because fuels are measured and sold in varying units of measure, cost comparisons of greenhouse heating fuels are usually based on what it costs to produce 1 million British Thermal Units (BTUs) of heat. The BTU is the standard measure of heat in the United States.
The price of traditional carbon-based fuels is volatile, and growers are becoming more concerned about farm practices and their impact on a changing climate. For these reasons, some greenhouse producers have moved to the alternative of biomass fuels. Biomass fuels are solid fuels derived from biological materials. Common examples are firewood, wood pellets, and wood chips. Biomass fuels are considered a renewable fuel source, but critics point out that they burn less efficiently than gas, coal, and oil. It is true that biomass fuels emit more CO2 per BTU compared to fossil fuels, but that is balanced by the fact that CO2 was captured and stored in the biomass as it was growing. Biomass fuels that are used on a small scale and sourced responsibly from wood residues and waste material are much closer to carbon neutral than sequestered carbon-based fuels (USEIA, 2021). Heating equipment that burns biomass fuels usually costs more than systems that burn oil and gas, but if a source of biomass fuel is available and comparable in cost per BTU to fossil fuels, it may be worth the expense to install a greenhouse heating system that can utilize biomass fuels.
The USDA has a free, online software tool called Virtual Grower that can be used to simulate the energy needs of a greenhouse structure. A grower can enter heating and lighting system details and greenhouse design details to simulate the energy needs of the structure. Different heating systems can be compared to help make decisions on upgrades. See the Further Resources section for links to this tool and a greenhouse energy self-assessment tool.
Cooling Systems
Traditionally, ventilation fans have been used to lower the temperature in greenhouses. If fans are used for ventilation, choosing energy-efficient models will reduce operating costs. The efficiency rating of agricultural fans is determined by the air flow in cubic feet per minute (cfm), divided by the rated wattage of the fan, written as cfm/w. The higher the value of this ratio, the more efficient the fan. The Bioenvironmental and Structural System (BESS) Laboratory at the University of Illinois tests agricultural fans, and the results are available online (see the Further Resources section). This testing and reporting helps growers choose higher-efficiency fans. Horizontal airflow fans (HAF) placed throughout the inside of the greenhouse cool through convection but are also very helpful in reducing heating costs by distributing air in a heating situation.
Natural ventilation systems (covered in the Conservation Measures section below) are increasingly the preferred method of ventilation in new greenhouses because of cost savings over fan ventilation. With motorized roll-up sides and roof vents being used instead of fans, a cost savings of more than $300 a year can be seen in a typical 30-foot by 100-foot greenhouse (Bartok, 2022). If natural ventilation is used to cool the greenhouse, it’s recommended not to run HAFs because they can inhibit the natural flow of air.
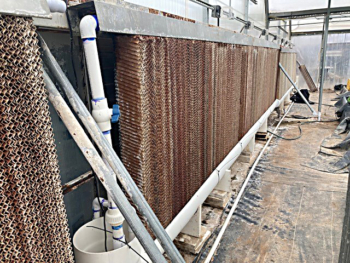
This evaporative greenhouse cooler’s paper-like mat absorbs and evaporates water along one end wall of the greenhouse. Photo: Chris Lent, NCAT
In some parts of the country, when summer temperatures are so high that ventilation and shading can’t provide adequate cooling, evaporative cooling systems are used to cool greenhouses. Most often, a pad-and-fan system is used, with water-soaked, paper-like pads or mats installed on the end wall closest to the summer prevailing wind. Ventilation fans on the opposite end wall pull moist air from the pads, and this air then picks up heat as it travels through the house and out of the exhaust fans. Evaporative cooling systems work best in conjunction with a well-designed ventilation system that reduces heat gain from the sun (University of Georgia Extension, 2014). In addition to the pad-and-fan system described above, high-pressure misting systems are also sometimes used.
With volatile fuel costs and concerns about greenhouse-gas emissions and climate change, some farmers are focusing on energy conservation and alternative heating and cooling methods for their greenhouses. First, we will consider the conservation measures that can be used to reduce energy needs in greenhouse production. Then, we will talk about both passive and active solar greenhouse systems and geothermal heating systems.
Greenhouse Energy Conservation Measures
With energy being one of the top costs associated with greenhouse produce, it is important to consider taking advantage of solar radiation and other energy-conservation measures to cut fuel expenses. Greenhouse heating can consume 75% of annual energy usage, so implementing conservation measures that impact heating can typically show a ROI of just a few years. These include reducing air infiltration, installing energy curtains, insulating sidewalls and the foundation perimeter, making good use of growing space, and installing electronic environmental controls (Bartok, 2015).
It is standard now for commercial greenhouses to use a double layer of polyethylene film with air space maintained between the layers by using a small, electric inflation blower. This provides an insulating air layer that reduces heat loss. Some other basic ways to conserve energy are to use shade covers and insulating thermal curtains. Installing shade cover over the greenhouse glazing reduces heat gain and can lower cooling loads by reducing the running time of evaporative cooling systems and ventilation fans. During heating months, up to 80% of the energy to keep the greenhouse warm is consumed at night, so thermal curtains are effective at reducing energy costs (Sanford, 2011b). Curtains are usually installed on the inside of the glazing, but where snow is not an issue, they can be installed on the outside. Curtains are closed at night to reduce heat loss overnight and opened again in the morning to take advantage of the sun. Certain types of thermal curtains can double as shade material in hot weather. The choice of glazing or plastic covering is very important. Infrared (IR) and anti-condensate (AC) plastic will save between 10% and 20% in fuel use by trapping the infrared radiation and preventing it from escaping at night (Bartok, 2022).
Greenhouse design can reduce energy costs by helping to regulate high temperatures. Open-roof greenhouses vent hot air from the top of the structure, while cooler air moves in through side-wall openings. On most days, when there is at least a one-mile-per-hour wind speed, natural ventilation can keep the air inside the structure within a few degrees of the outside temperature (Bartok, 2015). In addition, if cooling is the main consideration, prevailing winds should be considered to determine the orientation of the greenhouse.
Locating a new greenhouse in an area sheltered from the wind or installing wind breaks around an existing greenhouse to slow the prevailing wind can also improve heating efficiency. Routine cleaning and maintenance of heating equipment and checking the accuracy of thermostats are also important measures to take. Electronic thermostats are more accurate than mechanical ones and should be used for control of heating and cooling systems. Electronic controls should also be used for irrigation, humidity, and lighting systems controls.
Sectioning off and heating only part of a greenhouse for seed starting or building a germination chamber to delay the seasonal heating of an entire structure are simple management techniques that can save fuel. Depending on the current state of a greenhouse, any one or combination of these conservation measures could have an impact on fuel costs and a favorable ROI. For more information on conserving energy, you can find a Greenhouse Energy Conservation Checklist in the Further Resources section.
Passive Solar
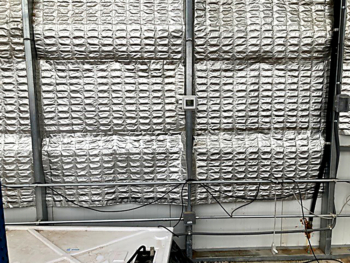
The phase change material shown here, installed on the back wall of a solar greenhouse, is at least five times more efficient at capturing and releasing heat than
traditional thermal-mass materials. Photo: Chris Lent, NCAT
Passive solar greenhouses are designed to capture and store heat from the sun and release it passively to keep the inside temperatures from dipping too low at night or during cloudy days, with low or no additional energy inputs. Thermal-mass materials like water, cement, or the earth itself are used inside the structure to absorb extra heat from the greenhouse on sunny days. These materials then release that stored heat when the sun goes down. In much the same way, phase change material (PCM) is used to store heat during the day and release it when temperatures cool at night. PCM used in greenhouses, most commonly made of paraffin wax, takes advantage of latent energy by absorbing heat when a material changes from a solid to a liquid, and then releasing that heat when the material changes back into a solid. PCM materials are more efficient than thermal-mass materials that have traditionally been used in passive solar greenhouses, such as water or masonry. The PCM materials store five to 14 times more heat for the same volume of material (Sutterlin, 2011).
The effectiveness of a passive solar greenhouse relies on an airtight structure that is well insulated on the north, east, and west-facing walls. Insulation, such as a retractable thermal blanket, can also be added to the south-facing glazing material at night. The structure should be oriented as close to true south as possible, with the glazing set at an angle equal to the location’s degrees of latitude plus an additional 15 degrees. That angle allows the low winter sun to hit the glazing at the optimal angle for heat gain inside the structure. Solar greenhouses are usually also built to a ratio of one wide to two long to one high, to optimize the planting-space-to-perimeter ratio. For example, a 12-foot-wide structure would be built 24 feet long and 12 feet high at the back wall. All these design features add up to a greenhouse that can maintain minimum temperatures above freezing even in the northern parts of the country (Thomas et al., 2003).
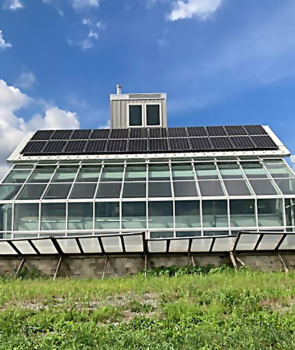
This passive solar greenhouse on Gib’s Farm in Pennsylvania includes a thermal mass wall, steep-angle south-facing glazing, and a solar chimney for airflow and cooling in hot weather. Photo: Chris Lent, NCAT
China remains the leader in passive solar greenhouse production, with more than 9.1 million acres in production at the end of 2017 (Liu et al., 2021). The Chinese solar greenhouse design incorporates all of the passive solar design features mentioned above but is unique in that the metal support ribs are built for extra strength, allowing them to span large widths from the back thermal mass wall to the front edge of the greenhouse (Bomford, 2010). This increases the growing-area-to-perimeter ratio even more. These systems rely on insulation blankets that cover the glazing at night to hold in the heat. While there are online sales of this type of greenhouse that ship from China, as of this writing, the authors were not able to find any distributors of these style greenhouses in North America.
Active Solar
Active solar heating systems use pumps or fans to actively move liquid or air through a solar collector to absorb heat from the sun. This heat is then stored for later use. One type of active solar system that farmers have experimented with for years is solar hot water, and another that is starting to be incorporated into greenhouses to help with heating is the climate battery.
Solar Water Heating
There are a few different designs for heating water with solar energy for the purpose of heating a greenhouse. Most utilize solar thermal panels that heat a water/glycol mixture that is circulated through a heat exchanger to store the heat in a large tank of water, called a solar storage tank. Another heat exchanger is used to extract heat from the solar storage tank and circulate it through radiant tubing under growing beds or tabletops. Some of these systems have been prone to leaks and inefficiencies that required heavy reliance on additional heating sources. However, some have worked well. Don Bustos from Santa Fe, New Mexico, has a solar water-heating system that enables him to produce crops year-round. A profile from the Sustainable Agriculture Research and Education (SARE) program explains Don’s farm energy-conservation practices.
Case Study: Santa Cruz Farm
Heating a greenhouse with solar power was a logical choice for Don Bustos, who incorporates principles of sustainability throughout his three-and-a-half acres of certified organic land in the small town of Santa Cruz. “I wanted to be lighter on the earth and use energy more consciously,” said Bustos, who farms more than 72 varieties of horticultural crops, including blackberries, raspberries, strawberries, tomatoes, squash, peppers, and braising greens.
Bustos also had a powerful economic incentive: One winter, he received a $700 gas bill for one month’s heat for the greenhouse. After researching solar options, Bustos eventually decided to install a root-zone thermal heating system, partially funded by a SARE grant.
To minimize costs, Bustos was able to pick up recycled solar collectors from a building demolition site. The panels sit 12 feet from the greenhouse, facing due south and at a 45º angle to maximize exposure to the winter sun. The panels generate enough heat to raise a glycol/water mix to approximately 200ºF. This heating fluid runs through a closed-loop system of copper tubing to an underground tank just a few feet away from the panels. The tubing is buried to a depth of seven feet to take advantage of the earth’s natural insulating properties. A heat exchanger raises the tank’s water temperature to 180ºF. The water then flows through the plastic tubes under the greenhouse’s beds, raising root-zone soil temperatures to a comfortable 48 to 52ºF.
The first season was extremely successful, cutting annual heating costs from $2,000 to $0, and increasing yields 30 to 40% above those from the standard cold frame. The only ongoing cost related to the solar heating system is a $5 monthly electricity charge for the two pumps that circulate the heated water from the underground tank through the greenhouse.
Thanks to the solar-heated system, Bustos can now produce a steady supply of salad greens, arugula, Swiss chard, kale, carrots, and radishes from October to March, even when outside temperatures drop below freezing. During the most frigid nights, Bustos blankets the beds with sheets of polyester, creating heat-retaining igloos. The system even works in reverse: When the soil is too hot during summer, Bustos runs the pumps to circulate water, now cooled by the geothermal properties of underground storage.
Excerpted from: Solar Energy for Sustainable Year-Round Production. (Western SARE, 2011)
Climate Battery
Another type of active-solar greenhouse heating system is the climate battery, sometimes referred to as an earth battery. A climate battery is installed to capture excess heat and store it in the thermal mass of the ground beneath the greenhouse, so that heat can be used in the winter months to help heat the greenhouse. These systems use fans or blowers to circulate the excess heated air in a greenhouse through perforated pipes buried in the soil below the greenhouse. This warms the soil and stores heat that is then transferred back to the greenhouse when heat is needed. Because these systems also take advantage of the steady temperature of the earth, they are considered a type of geothermal system. Climate batteries also can help keep structures cooler on hot days and remove excess moisture from the air inside the greenhouse.
There is not much research or data on the economic viability of climate batteries. Their effectiveness can depend on many factors, such as the location and design of the greenhouse, how the battery was designed and installed, and the materials used to bury the pipes. For more information and resources on active and passive geothermal greenhouse systems, including design features, components, and costs, see the ATTRA publication Geothermal Greenhouses: Exploring the Potential. And for design features and research results on the effectiveness of an installed climate battery, see the Hip Peas Farm case study below and visit Threefold Farm’s PSU Climate Battery case study, listed in the Further Resources section.
Case Study: Hip Peas Farm, Hooksett, New Hampshire
At Hip Peas Farm, a climate battery system was installed for a 30-foot by 96-foot high tunnel. The tunnel has a gothic peak and was composed of inflated double-layer polyethylene for the top and sidewalls, and a triple-wall polycarbonate for each end wall.
Manifolds being connected by flexible pipes. Photo: Dan Birnstihl, NCAT
Prior to installation of the tunnel, the site was excavated to a depth of four feet, and a base of crushed stone was laid on the bottom of the pit, roughly three to six inches thick. A 15-inch diameter rigid, corrugated pipe was run along the inside of each end wall, about three feet from each end, and 22 rows of 1-inch perforated, flexible pipes covered in fabric “socks” were run from one end to the other, each separated by about 16 inches, connecting the two 15-inch manifolds. Once attached, all lines were secured with liquid cement to prevent air leakage at the connection points. The perimeter was lined with 4-foot by 8-foot, one-inch-thick rigid insulation boards, starting from the top of the soil line, down to a 4-foot depth, and the first layer was covered by about a foot of crushed stone. Landscape fabric was installed over the first layer, and a second layer of manifolds, pipes, and stone was installed on top of the first, then covered with landscape fabric, pipes for a radiant heating system, and about a foot of topsoil where crops would be planted.
A Northeast SARE (Sustainable Agriculture Research and Education) grant was awarded to examine the temperature differences between this tunnel and a control tunnel installed next to this one that had every feature except the climate battery system. From November 2020 through December 2021, air temperature and relative humidity (RH) were monitored in each tunnel, as was soil temperature. Outside air temperature and RH data collection started in December of 2020. At the time of the completion of this publication, the project is still ongoing.
Comparison of average air temperatures. Outside air temperature was not collected in November2020. Differences in air temperature were statistically significant (p ≤ 0.05).
On average, the air temperature in the climate battery tunnel (CB tunnel) was 3º warmer compared to the control tunnel, the difference of which was statistically significant (P ≤ 0.05). Over the total time the temperatures were reported, the heat difference between the climate battery tunnel and control tunnel was roughly 716 million BTU.
Although RH readings were taken, the differences were not as stark, with the CB tunnel averaging 93.2% RH and the control tunnel averaging 94.7% RH. Like the air temperatures, average soil temperatures were also higher in the CB tunnel (42.1⁰ F) than the control tunnel (40.2⁰ F). At the time of this writing, statistical analysis has not yet been performed on these data.
The total cost of the climate battery was $18,000. This broke down to $7,500 in materials like insulation and ducting, $4,000 in excavation, $4,000 in crushed stone, $1,100 in fans, and $2,000 in labor. Growers at Threefold Farm in Pennsylvania had an analysis of their climate battery systems performed by Penn State University. Their experience suggests that the fill removed from the site would have been a better material to use than crushed stone, as stone has the highest insulation value but does not transfer retained heat as well. In this instance, if the materials that were removed during excavation were used to cover the pipes, the cost of the crushed stone would have been saved, lowering the cost of the battery to $14,000.
Further improvements to the design were also noted in the PSU studies that could increase the efficiency of the system. Splitting the tunnel into thirds and creating three separate 25-foot by 25-foot blocks, each containing its own manifolds and fans, would decrease the volume of air that would need to be moved by the fans and blowers, thus making the system more efficient. The PSU study also suggests an alternative orientation utilizing two manifolds and four layers per block. A visual rendition of their suggested design can be found on the Threefold Farm website. In addition, fans were utilized for the climate battery at Hip Peas Farm, where blowers may have been a better choice for intake. Blowers on average are more expensive than fans, however, and would increase the overall cost of the system.
Preliminary results on the effectiveness of climate battery systems to reduce heating and cooling cost in greenhouses are promising. However, more research still needs to be done to determine the financial efficacy of these systems. To learn more about this SARE study, visit the project page on SARE’s website.
Organic Certification
The USDA Agricultural Marketing Service manages the National Organic Program (NOP), which regulates organic certification in the United States. NOP’s Introduction to Organic Practices tipsheet describes organic agriculture as “the application of a set of cultural, biological, and mechanical practices that support the cycling of on-farm resources, promote ecological balance, and conserve biodiversity. These include maintaining or enhancing soil and water quality; conserving wetlands, woodlands, and wildlife; and avoiding use of synthetic fertilizers, sewage sludge, irradiation, and genetic engineering. Organic producers use natural processes and materials when developing farming systems—these contribute to soil, crop and livestock nutrition, pest and weed management, attainment of production goals, and conservation of biological diversity” (USDA-AMS, 2021).
The organic transition process requires careful planning and adjustments to a new management system, as well as outlining an Organic System Plan. The new management system will require adjustments in fertility, pest management, labor, and recordkeeping requirements. Considerations of new marketing channels, pricing, and labeling also need to be thought through. Organic certification can be costly. Certification cost-share programs can offset a portion of certification expenses. Other USDA agencies, such as NRCS, offer some assistance and incentives for transition to organic. Talk with your certifier about the length of the transition period for your operation. While this is one of the standards that needs further clarification, transition times may vary based on prior production practices and materials used, especially for container or non-soil-based operations, which are often utilized in greenhouse production. For more information about the organic certification and transition process, see the Organic Farming topic area of the ATTRA website.
Can Hydroponics be Certified Organic?
Hydroponics is a method of growing plants using nutrient solutions in water, without soil. Hydroponic and aquaponic produce is typically grown in perpetually flowing water in which nutrients are dissolved, and supported typically in an inert medium, such as perlite, gravel, biochar, or coconut husk. In the United States, some farms using these methods use fertilizers and pest-control practices that can be certified organic through the USDA National Organic Program (NOP). USDA organic regulations do not currently prohibit hydroponic production, although it is prohibited in European countries. In a 2018 statement, NOP declared that “certification of hydroponic, aquaponic, and aeroponic operations is allowed under the USDA organic regulations…” (USDA-NOP, 2018). USDA also noted that the NOSB recommended prohibiting aeroponics and further stated its intent to consider this recommendation. As of November 2020, USDA had not initiated any action on this recommendation (National Agricultural Law Center, 2020). Organic hydroponic production is allowed as long as the producer can demonstrate compliance with the USDA organic regulations to the certifier.
Although NOP is considering specific standards for organic hydroponic operations, there is no proposed rule at this time. Because of this, there is a lack of organic standards to guide organic inspectors for production facilities, and lack of consistency in how accredited certifiers review them. In the meantime, hydroponic operations certified under NOP must comply with the organic crop regulations as they are written. Accredited certifying agents certify organic hydroponic operations based on the current organic regulations and the operation’s Organic System Plan. In the future, NOP may provide additional guidance regarding organic hydroponic production and how the regulations apply to such methods.
If you are considering seeking USDA organic certification of your hydroponic operation, check with your intended certifier regarding its interpretation of USDA regulations—what is allowable and not allowable in its interpretation—before you get started with the certification process. Many certifiers interpret the standards to require crops to be grown in soil in order to comply with the USDA regulations. Organic certification of crops grown using hydroponic or aquaponic methods remains controversial. At the heart of the discussion is the central question of the role of soil in organic production, and whether soilless systems are compatible with organic production.
Fertility and Soil Management
ATTRA publications that explain sustainable fertility management in more detail include Managing Soils for Water: How Five Principles of Soil Health Support Water Infiltration and Storage and Alternative Soil Amendments.
Although the process can be more complicated than it is in the field, it is possible to obtain adequate nutrients from organic sources in a greenhouse, but it takes careful and creative management. No single fertilizer will provide all of the essential elements required, but a combination of organic products can be devised. Greenhouse nutrient availability can vary widely, depending on the materials applied and the environmental conditions that affect microbial activity in the greenhouse environment. Many organic growers rely on crop rotation with cover crops to manage soil fertility, organic matter, and pests. It is harder to do this in a greenhouse, where space is at a premium.
Most non-hydroponic greenhouse growers produce their crops in soil in bags, in raised beds, or in the ground. In those situations, fertility management is similar to outside production, with many nutrients obtained through building organic matter with compost, manure, or peat and supplemental organic granular fertilizers. Table 1 contains a list of common granular fertilizers used in organic greenhouse production.
Douglas Cox, from the University of Massachusetts School of Agriculture, suggests using a granular slow-release fertilizer initially with greenhouse crops, then supplementing with a liquid fertigation after 30 days. His research has shown that greenhouse crops tend to get ammonia toxicity, which is represented with interveinal chlorosis in the plant. “This chlorosis is most likely caused by an accumulation of too much ammonium-nitrogen in the plant, so-called ‘ammonium toxicity.’ Most greenhouse crops do best with a combination of ammonium and nitrate nitrogen. Unfortunately, organic fertilizers generally don’t contain nitrate-nitrogen” (Cox, 2014).
Table 1. Preplant Organic Fertilizers | ||
Fertilizer Material | Estimated NPK | Nutrient Release |
Alfalfa meal | 2.5-0.5-2.0 | Medium-fast |
Blood meal | 12.5-1.5-0.6 | Slow |
Cottonseed meal | 7.0-2.5-1.5 | Slow-medium |
Crab meal | 10.0-0.3-0.1 | Slow |
Feather meal | 15.0-0.0-0.0 | Slow |
Fish meal | 10.0-5.0-0.0 | Medium |
Granite meal | 0.0-0.0-4.5 | Very slow |
Greensand | 0.0-1.5-5.0 | Very slow |
Bat guano | 5.5-8.6-1.5 | Medium |
Kelp meal | 1.0-0.5-8.0 | Slow |
Dried manure | Variable | Medium |
Seabird guano | 12.3-11.0-2.5 | Slow-medium |
Rock phosphate | 0.0-18.0-0.0 | Slow-very slow |
Soybean meal | 6.5-1.5-2.4 | Slow-medium |
Wood ash | 0.0-2.5-5.0 | Fast |
Worm castings | 1.5-2.5-1.3 | Medium |
Applying liquid fertilizer through irrigation lines—a technique known as fertigation—is a common practice in greenhouse production. Nitrogen and phosphorus are the two primary nutrients injected through fertigation systems. Fertigation can provide supplemental doses of these nutrients, especially at critical periods during the growing season, such as fruiting. Fertigation is not a substitute for a complete soil-based fertility program and must be considered part of the overall nutrient-management plan for the greenhouse. In order for fertigation to be effective, the fertilizer must be completely soluble, or else it will clog emitters. There are many organic soluble fertilizer options these days. To calculate the cost of greenhouse fertilizer products, the organic fertilizer calculator developed by Oregon State University and listed in the Further Resources section might be useful (Miles et al., 2015).
Table 2 is reprinted with permission from Lynette Morgan’s Organic Soilless Greenhouse Systems (2021). The table lists different nutrient deficiency signs and organic-based remedies and is very helpful for troubleshooting nutrient deficiencies in an organic greenhouse operation.
Table 2: Organic Strategies for Nutrient Deficiencies* | ||
Element | Deficiency Symptoms | Remedy |
Nitrogen (N) | Old leaves turn pale green then yellow with reddish veins and midribs. Stunted growth. | Dried blood, fish meal, or guano extracted in water. Add greater amounts in your next compost batch. |
Phosphorus (P) | Stunted growth, dull green leaves with purple tints. Old leaves scorch at the edges and wither early. Early, premature bolting. | Add reactive rock phosphate, calcium phosphate, or extract of guano in solution. Add greater amounts of guano, bone meal, or fish meal to the next compost batch. |
Potassium (K) | Small, dark, bluish-green, glossy leaves, curving slightly backwards. Old leaves with yellow patches, scorched edges cured upwards. Small root system. | Add more kelp extract to the nutrient solution and potassium sulphate. Add greater amounts of ashes to the next compost batch. |
Calcium (Ca) | Young leaves cupped backwards, with white spots around the edges. These later turn brown. Forward rolling of the leaf margin. | Calcium is often naturally occurring in water supplies, particularly `hard water’ sources. Add lime to the solution. Add greater proportions of bone meal, gypsum, or dolomite to the next compost batch. |
Magnesium (Mg) | Leaves become bronzed, and later, yellow patches appear between the leaf veins. | Add dolomite or serpentine, or magnesium sulphate in solution. Add greater amounts of dolomite, and animal manures to the next compost batch. |
Sulfur (S) | Purpling of old leaves, which then shrivel. Young leaves small and yellow between the veins. | Sulfur, potassium sulphate or magnesium sulphate in solution. Greater proportions of gypsum and poultry manure required in the next compost batch. |
Manganese (Mn) | Veins stand out clearly with yellow in between. As the plant ages, small dead spots and papery areas appear. Slow root growth. | Add extra kelp extract or manganese sulphate. |
Boron (B) | Split or thin misshapen roots. Roots with torn patchy surface and dull skin. | Add extra kelp extract, Borax or ‘Solubor.’ |
Iron (Fe) | Very pale leaves, especially the youngest early in the season. Veins stay dark. | Add more kelp extract, iron citrate, or iron sulphate. |
*Reprinted with permission from: Morgan, Lynette. 2021. Organic Soilless Greenhouse Systems, Chapter 7 in: Hydroponics and Protected Cultivation – A Practical Guide. CAB International, Oxfordshire UK, pp. 100-114. |
Salinity is more apt to become a problem in greenhouses than in the field because the soil is not exposed to large rain events that flush it of salts that build up from application of manure, compost, and fertilizers. With greenhouse space being at a premium, it is difficult to practice crop rotation, but a study on salinity and soil quality in greenhouse systems showed that yields decrease significantly after five subsequent years of the same crop in greenhouse vegetable systems. In addition, the soil organic matter and soil organisms decreased and salinity increased. The highest yields were seen with a cover crop in the rotation, but that can be difficult in greenhouse settings. It may be necessary to water the greenhouse post-cropping with a sprinkler, to leach the salt through the soil profile. Salinity seems to be more of a problem when continuous cropping is practiced in the greenhouse (Liang et al., 2013; Gougoulias, 2011).
Case Study: Five College Farms
By Daniel Prial, NCAT
Approaching Five College Farms early in the morning, it is easy to see the red LED grow lights that nourish the plants. Photo: NCAT
Five College Farms is a two-acre, 52,000-square-foot, organic vegetable greenhouse operation in Hadley, Massachusetts. The current owners converted a former plant nursery into a source for locally grown greenhouse produce – specifically Persian cucumbers and heirloom tomatoes. Although in business for less than five years at the time of writing, the company already has sales exceeding a million dollars. The costs for maintaining an organic greenhouse operation, however, are equally high.
Business Manager Arthur Mulyono. Photo: NCAT
The vegetables at Five College Farms grow in long troughs, full of soil, worms, beneficial insects, and more. The farmers are proud of their living growing medium. All of their fertilizers and amendments are plant-based. Arthur Mulyono, the farm business manager, likes to joke that Five College Farms is a “veganic” operation.
To understand the needs of their plants, Five College Farm has a contract with a laboratory in the Netherlands to analyze the plants’ sap. They take old leaves and young leaves from scattered plants in their greenhouse and ship them out every other week during the growing season. This provides immediate knowledge about the health of their operation and lets them provide exactly what the plants need at any given point in time. The sap analyses they receive tell them levels of sugar, potassium, calcium, magnesium, sodium, ammonium, nitrogen, and much more. To meet the plant needs, Five College Farms selects from a large list of agricultural chemicals approved by Baystate Organic Certifiers – their Massachusetts organic certification program.
Rows of cucumbers grow toward the ceiling and are
nourished by red LED grow lights. They are protected
by yellow tape strips that monitor greenhouse pests.
Hanging from the ceiling further back is a blue carbon
dioxide machine – burning natural gas to raise the
carbon dioxide level in the greenhouse for the plants.
Between the troughs of plants are rails to move the
machinery. Photo: NCATControlling pests in the greenhouse is a combination of identifying and reacting. Within and above the lines of plants are large colored strips of tape. Yellow tape attracts most pests and blue tape attracts thrips, specifically. The farm also brings in an intern from one of the local colleges to take regular inventory of the insect pests in the greenhouses. Then, based on their results, they refer to a similar list of agricultural chemicals and manage their pest issues. The costs compile quickly. Treating every other plant in a 10,000-plant greenhouse with a sachet of beneficial insects to control spider mites, for example, can cost in excess of $6,000 per week.
The Five College Farms greenhouse soil. Photo: NCAT
Making back those costs means selling a premium product at a premium price. This is further complicated because Five College Farms sells wholesale directly to regional grocery stores and food co-ops like Wegmans, Whole Foods, and Big Y. In order to compete with organic greenhouse produce from Mexico and Canada, Five College Farms focuses on their local roots. They sell a Massachusetts-grown product. Still, they often need to get into grocery stores and deal directly with the end-consumer. They routinely do product demos, offering free samples of their tomatoes and cucumbers. Because of the taste of their heirlooms, they can be an easy sell. The cucumbers, however, need more advertising. In the end, they rely on their two biggest strengths: they are local to New England, and they are a fully organic greenhouse operation.
Composting plays a big role in nutrient management for all organic farms. This is no exception with greenhouse nutrient management. Not all compost is created the same, however. If you are purchasing compost, be sure to know the nutrient and salt content of the final product. Also, it is helpful to know the products that are used in the composting process. Many composts sold as “biosolids” are comprised of composted sewage sludge. Not only do these products often contain trace heavy metals, but they are also prohibited for use in organic production. For more information on using compost in a greenhouse production system, see the Cornell University video Floricast: Understanding compost, vermicomposts, and teas in the Further Resources section.
Cover crops can fit nicely into greenhouse ground cultures that include a crop-free rest period (in summer, for example), if you are willing to give up the premium space. Short-term cover crops include some legumes, buckwheat, annual ryegrass, oats, rapeseed, and oilseed radish. Often, the choice of cover crop will depend on the vegetable rotation and the intended purpose. Cover crops can replenish and help build organic matter in soils, increase microbial activity, add nitrogen, and help prevent or suppress diseases and nematodes, especially when brassica and oilseed radish cover crops are used.
In a study on cover cropping in greenhouse cucumbers in Turkey, the researchers found that the green manuring (cover crops grown solely for fertility) improved the organic matter and nitrogen content of the soils. When they analyzed the other available nutrients in the soil, these were found to be sufficient, as was the nutrient content of the cucumbers. They recommended pea and vetch as efficient winter green-manure crops for vegetable production in greenhouses. Poultry manure also produced positive effects, in particular on soil total N content. Therefore, it could be used with green manure crops based on the nitrogen content of the soil (Tuzel et al., 2013).
To increase soil fertility, Living Web Farms always has a cover crop growing somewhere in its greenhouse. The growers section off crop production with cover crops in their greenhouse. This rotation strategy can be seen in the Living Web Farms video Unusual Cover Crops in the Greenhouse in the Further Resources section. “We try to give each bed one season in cover crops. This greatly helps with disease issues, which are major problems when you keep growing the same crops repeatedly,” says Patryk Battle, director of the nonprofit educational and research farm.
Table 3 is from an eOrganic article that identifies cover crops that are useful for hoophouse production, which is also applicable to soil-based greenhouse production.
Table 3. Suitable Cover Crop Varieties for High Tunnels | ||||
Function | Legumes | Grasses | Brassicas | Other |
Winter Kill | Cowpea (Vigna unguiculata) | Oats (Avena sativa) | Tillage radish (Raphanus sativus) | |
Japanese Millet (Echinocholoa esculenta) | ||||
Overwintering | Hairy vetch (Vicia villosa) | Winter rye (Secale cereale) | Most brassica cover crops are not reliably winter hardy in northern regions. | |
Red Clover (Trifolium pratense) | Winter wheat (Triticum aestivum) | |||
Field pea (Pisum sativum) | ||||
Subterranean clover (Trifolium subterraneum) | ||||
Crimson clover (Trifolium incarnatum) | ||||
Summer Planted | Cowpea | Sudangrass (Sorghum bicolor (L.) Moench) | Tillage radish | Buckwheat |
Sunn hemp (Crotalaria juncea) | Sorghum-sudangrass (Sorghum × drummondii) | |||
Spring Planted | Hairy vetch | Winter rye | Tillage radish | |
Clovers (Red, White, Sweet, Crimson, Berseem) | Spring wheat (Triticum aestivum) | |||
Oats | ||||
Intercrops/ Pathway Crops | Clovers (Red, White, Sweet, Berseem, Crimson) | Fescues (Festuca spp.) | ||
Perennial ryegrass (Lolium spp.) | ||||
Winter rye/ Cereal rye | ||||
Perkus, E. et al. 2019. Options for Including Cover Crops in High Tunnel Rotations in the Northern United States. |
Weed Management
Strategies for non-herbicidal weed control inside a greenhouse include a combination of hand hoeing, mechanical cultivation, steam pasteurization, soil solarization, and mulching (fabric, plastic, or organic mulches).
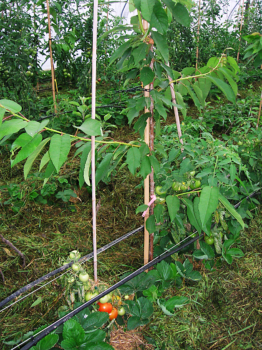
Weed control in ground culture systems. Hoch Orchards mulches with grass from mowing its orchards in its hoophouse that grows cold-sensitive fruit. Photos: NCAT
Plasticulture in greenhouses, especially black plastic, is quite common for many types of greenhouse vegetables because it also increases the soil temperature, allowing crops to be planted earlier and capturing the off-season prices that are essential for greenhouses. NOP’s standards require removal of the plastic after each growing season. Paper mulches are allowable by the NOP and, of course, certain cardboard and newspaper are allowable. The paper tends to decompose and is difficult to pick up after the season is over, which makes it difficult to till. At this time, no biodegradable plastic mulch is allowed for use on organic farms. Although biodegradable plastic mulch may meet the NOP biodegradability requirements (90% biodegradation within two years), currently no products have been approved for use in certified organic production because, so far, none meet the requirement of being completely biobased (Miles et al., 2017).
The practice of “occultation,” or tarping, has been used inside and outside greenhouses with anecdotal success. The ground is watered, and then a black tarp is placed over the ground for at least a month. The weeds germinate with the moisture, then die due to lack of sunlight. This has a big impact on annual weeds, but less so on perennial weeds. For more information on tarping, see Lounsbury et al., 2022.
For more information on using mulches in organic systems, see the USDA Agriculture Marketing Services information sheet titled Allowed Mulches on Organic Farms and the Future of Biodegradable Mulch in the References.
Soil Disinfection
A major concern in covered-ground culture systems is soil sterilization, or pasteurization, for control of soil-borne pathogens. Methods of disinfection include solarization, steam, electrical heat, and biological control. For more information on soil steaming, see the ATTRA blog on Soil Steaming for Pathogen, Pest, and Weed Control in High Tunnels.
Solarization is a method of killing diseases and weeds through heating the soil to temperatures high enough to kill weed seeds and microorganisms. It is typically done using clear plastic placed over the soil. While this technique is more commonly used to kill disease organisms in the soil, it can also be effective against many weeds and their seeds. For example, studies have shown solarization to be effective on chickweed seeds. It is generally not effective against weeds with deep tubers or rhizomes, like perennial grasses, such as Johnson Grass.
Research conducted at UC Davis demonstrated the key principles for successfully solarizing weeds (Fennimore, 2018):
- Use clear plastic.
- Apply the sheeting during hot weather.
- Effective solarization requires good movement of heat into the soil. This is aided by high levels of soil moisture, so the soil should be irrigated before the plastic is laid down. Air gaps between the plastic and soil should be minimized, as they inhibit heat transfer into the soil.
- Solarize for at least four weeks for effective weed kill. This will vary according to the quality of plastic sheet used, the prevailing temperatures, and weed species present.
See the ATTRA tipsheet Soil Solarization and Biosolarization for more details on practicing soil solarization.
Pest Management
Although greenhouses reputedly keep out certain pests, there can be significant insect and disease problems in greenhouses if proper sanitation and IPM practices are not implemented.
Greenhouses provide a suitable environment for using biological control to manage pests. Many useful biological control agents, also called natural enemies, are commercially produced, and these can often be incorporated as a strategy for an organic integrated pest management (IPM) program within the greenhouse. Farmscaping with plants that attract pollinators and natural enemies between greenhouses can be used if the greenhouses are open to the outside for ventilation purposes. Growers can also do this within the greenhouse to support introduced natural enemies, particularly if they are growing cut flowers in the greenhouse.
When preventative and biological controls fail, certain organic-based chemicals can be used as a last resort. ATTRA’s Sustainable Pest and Weed Control Database can be used to find suitable products for organic management of most greenhouse pests. Organic pest management starts with understanding the pest’s life cycle.
For general information, see ATTRA’s Ecological Pest Management tutorial.
Disease Management
Although many diseases, especially foliar diseases that spread through wind and rain, are managed simply through utilizing greenhouse production, there is increased susceptibility in greenhouses for diseases that spread in high-humidity environments, such as botrytis and white mold. Like in the field, greenhouse diseases can be managed by employing appropriate integrated pest management (IPM) approaches, including cultural tactics, resistant varieties, and applications of materials approved for use in organic production systems. Crop rotations, cover crops, and high-quality compost application all work well for preventing greenhouse diseases.
Further, research has shown that increased organic matter results in a more extensive and varied microbial community, resulting in suppression of soilborne pathogens and improved plant health. Research from Ohio State University has shown that tomato plants grown in compost-amended soil in high tunnels had significantly less white mold than those grown in non-amended soil. Early blight was also reduced on tomatoes grown in compost-amended soil, compared to those grown in non-amended soil in high tunnels (Miller, 2018).
Environmental management of diseases includes air circulation and drip irrigation to avoid standing water on leaves. Also, avoid handling plants in the early morning when water has condensed on the foliage.
Variety or cultivar selection plays an important role in successful greenhouse vegetable production.
Cultivars often originate in greenhouse breeding programs where selection is based on disease resistance and ability to perform under greenhouse climatic conditions. Greenhouse-seed vendors and the Cooperative Extension Service can recommend appropriate cultivars. Another consideration in certified organic greenhouse production is that organic seed must be sourced, unless a specific variety or quantity is not able to be sourced from a certified organic supplier. There is no exemption for cost. As is mentioned in the Greenhouse and Hoophouse Grower’s Handbook, seed is an important investment and it pays to spend more for disease-free seed and greenhouse specific varieties (Mefferd, 2017), particularly for Good Seed and Plant Practices (GSPP) certification, which identifies seed grown to minimize pathogens. When purchasing seed, look for organic and GSPP varieties.
Grafting has been a disease-management technique in plants for years, mainly for tree fruits and ornamentals. Recently, it has been used in high-value vegetable plants such as tomatoes, cucurbits, and peppers. The aim of grafting is to combine and utilize beneficial traits of both the rootstock plant and the scion plant (the top plant that yields fruit).
A publication from the Cornell University Controlled Environment Agriculture program, titled A Guide to Grafting Tomatoes: Cornell’s Tips for Success, has several great tips for successful grafting.
Grafting Tips
(Source: Gagne et al., 2020)
Tip 1: Start with good seed. Poor-quality seed can lead to bad germination, increased risk of disease and inconsistent seedling growth — all of which will make grafting much more difficult.
Tip 2: Always run a small trial before using a cultivar for the first time. Sowing a few seeds and growing them to grafting size can help to determine the cultivar’s germination rate, growth rate, and consistency.
Tip 3: Seed the rootstock variety two days after the scion variety. Rootstock cultivars have vigorous growth and, therefore, grow faster and reach sufficient stem diameter for grafting earlier than scion varieties.
Tip 4: Choose a transparent grafting clip that is slightly smaller than the seedling stem diameter to allow for the union to be tight and to give more visibility to the grafted area.
Tip 5: When making the cuts, it is important to use a sharp surface, such as a new razor blade, recently sharpened knife, or new grafting blade placed on a grafting tool. Grafting tools are commercially available and help to ensure perfectly uniform cut angles.
Tip 6: For larger-scale grafting projects, a climate-controlled chamber with a fogging system that can achieve nearly 100% humidity can be used in place of the humidity domes.
Tip 7: The trays and humidity domes can be reused multiple times; however, it is crucial to thoroughly wash and sanitize them before reusing.
Although the grafting process can take some time and effort to perfect, the team at Cornell reports 95 to 100% success when using these steps. Grafting takes a lot of time, and the seeds can be expensive. It should be reserved for high-value crops. The recently published Greenhouse and Hoophouse Grower’s Handbook by Andrew Mefferd (editor of Growing for Market) has a detailed chapter on grafting. See the Further Resources section for information on purchasing this valuable resource.
Greenhouse Systems
Soil vs. Soilless Culture
Greenhouse production is based on either soil or soilless culture. In soil culture, vegetables are produced in the native soil or in soil brought inside the greenhouse and installed in a raised-bed system. Soilless culture, mainly hydroponics or aquaponics, is the production of plants in a soilless medium.
The categories of soilless culture are illustrated in the diagram below, with examples of the types of media used in each.
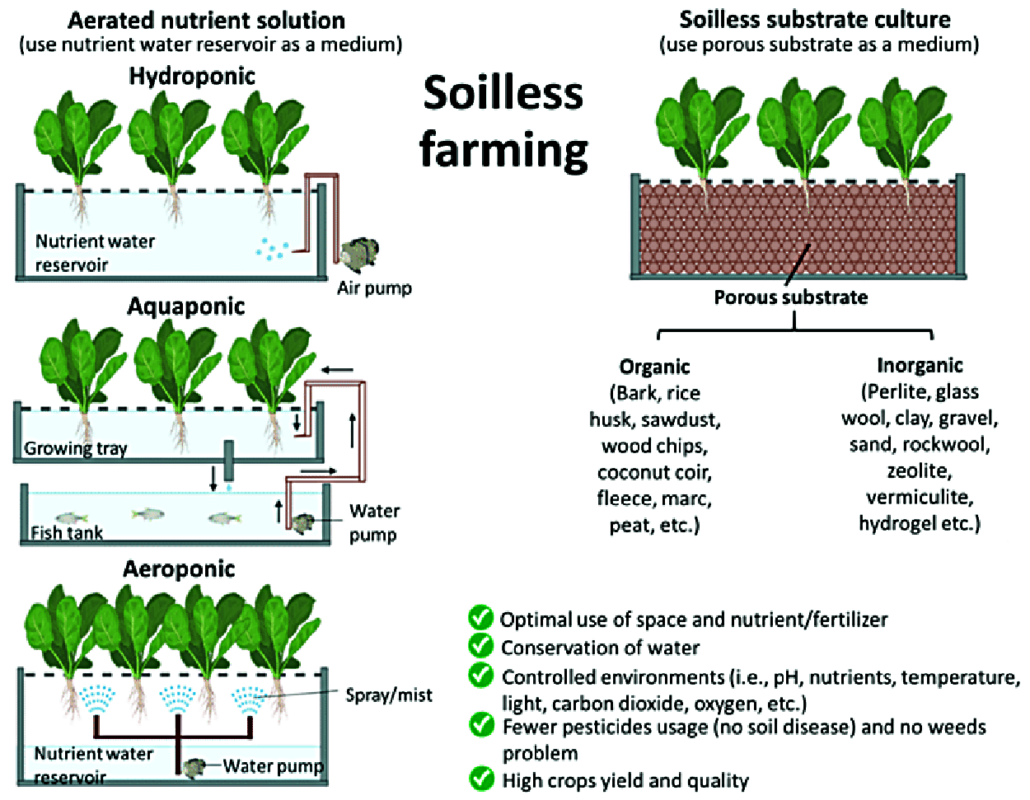
Source: Maluin et al., 2021. Creative Commons.
In 1974, 70% of U.S. greenhouse production was based on soil culture and 30% on soilless culture. A significant shift to soilless systems has occurred in the last decade. The most recent census data from 2019 shows that 53% of vegetables grown under protection are from hydroponic systems (USDA NASS, 2019). This is actually down from the 2014 census data, which had 60% in soilless culture. There are several reasons soilless culture became so popular:
- Elimination of fumigation and steam treatments for soil-borne diseases
- Ease of installation (once the initial installation is complete)
- Technical assistance available for soilless systems
- Fertility control through commercial soluble fertilizers
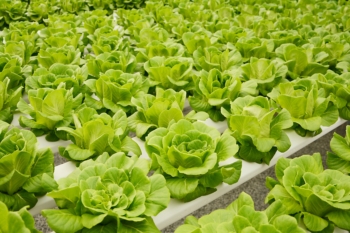
Hydroponic lettuce. Photo: NCAT
Although NOP has allowed the certification of hydroponic operations, there are many challenges for certified organic hydroponics, including developing approved substances that are soluble. The availability of approved soluble organic fertilizers in recent years has made it easier to grow crops hydroponically with organic-approved products. The sticking point is whether certifiers will acknowledge that organic production can be done without soil, since soil and organic soil management was a premise and intention of the original organic certification process. This is still very much the case in other parts of the world.
This publication has limited information on hydroponic production but is not an exhaustive resource. There are many existing resources available, and the Further Resources section of this publication lists a few key resources on hydroponic vegetable production.
Bag Culture
Bag culture can use soil or compost-based medium or soilless culture. Bag culture is when plants are grown in a medium contained in lay-flat or upright polyethylene bags (two to five gallons in size) and fed with liquid fertilizers through drip irrigation lines. Media can be peat/vermiculite, sawdust, rockwool, rice hulls, pine bark, peanut hulls, compost, topsoil, or mixes of any of those. Bag culture is adaptable to both aggregate hydroponics fed with liquid fertilizers and standard soil culture, in which the bulk of fertility is supplied through a compost-based potting mix.
Upright bags should be purchased at a greenhouse supplier. They usually contain one plant per bag. Lay-flat bags are closed and are made of 4-mil, UV-protected polyethylene and are typically pre-filled with substrate. Lay-flat bags often have two or three plants per bag. Bags are most often placed in double rows in the greenhouse.
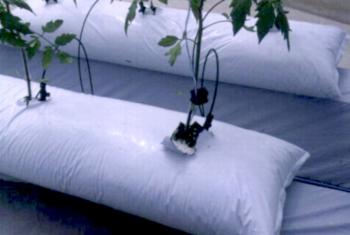
Lay-flat bag. Photo: University of Florida Agriculture Extension
Bag culture is well suited to the production of upright and vining crops like tomatoes, cucumbers, and peppers. Bag culture has become the preferred method of greenhouse vegetable production in many parts of the United States because it is easy to establish and manage successfully. One problem with bag culture is the potential for excess fertilizer solution to leach out of the drainage holes in the bags and into the greenhouse soil. Another is the disposal required for organic production.
Adapting bag culture to standard production in a certified organic greenhouse operation requires specially formulated organic potting mixes. An organic potting mix should not include any synthetic fertilizers or wetting agents and should be considered in the costs of production. Growers can purchase certified organic potting mixes from a commercial supplier or mix their own. Organic bag-cultured vegetables may include a combination of incorporated, top dressed, liquid-fed, and foliar-fed fertilization systems. See ATTRA’s Potting Mixes for Certified Organic Production publication for a summary of media and fertilizers that can be used in organic production systems.
Shallow-bed Culture
Shallow-bed culture, also known as thin-layer culture, is the production of sprouts or herbaceous herbs and vegetables in a thin layer—one to three inches in depth—of potting mix or compost laid on top of plastic mulch or woven weed barrier or in shallow containers. Herbaceous crops adapted to shallow-bed culture include specialty lettuces, greens, cresses, culinary herbs, and microgreens.
Microgreens are a great supplementary revenue stream for farmers. They can be grown with relatively little input and have a very quick turnaround time from seeding to harvest. The seed can be very expensive for specialty varieties of microgreens and should be accounted for in enterprise analysis.
Listen to the ATTRA podcast with Joe Martinez from Arizona Microgreens, describing their microgreen production and marketing strategies.
Hydroponics
In hydroponics, plants are grown in a soilless medium and fed with soluble fertilizers. There are two broad categories of hydroponics: liquid hydroponics and aggregate hydroponics. Hydroponics continue to be a contentious issue with organic greenhouse producers (see previous text box).
Liquid systems include the nutrient film technique (NFT), aeroponics, floating raft, and noncirculating water culture. Aggregate systems include inert, organic, and mixed media contained in bag, trough, trench, and bench setups.
Liquid systems like NFT are often managed as closed, or recirculating, systems. Aggregate systems are commonly managed as open, or flood-and-drain, fertigation systems.
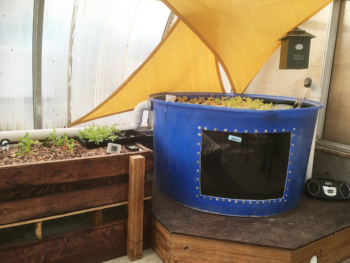
Aquaponics tank. Photo: NCAT
Aquaponics
Aquaponics presents a good solution to fertility in hydroponic greenhouses. See the ATTRA publication Aquaponics–Multitrophic Systems for Sustainable Food Production.
Vertical Farming
Vertical farming is probably the fastest-growing sector of the hydroponics industry, much of which was not grown in greenhouse conditions. Large-scale investments have enabled huge multi-level facilities to start in urban areas.
Investment is essential in these types of operations because of the high start-up and input costs, especially electricity. The formula that is currently working and profitable is plants that require low light intensity, short turn around, and high density (Adams, 2017).
It remains to be seen if vertical farms can be profitable. Most of these farms have investors, and their biggest costs are energy and labor. It is important to note that some of the largest vertical farming facilities have gone bankrupt in recent years.
Economics of Greenhouse Vegetable Production
Besides the initial investment of greenhouse construction, labor and energy are usually the two greatest ongoing greenhouse expenses. If you can find a way to decrease costs of either or both of these, your chances of making a profit will be strengthened. Sustainable Agriculture Research and Education (SARE) funded a study on the return-on-investment at Comida de Campos Farm in New Mexico. The goal was to produce tomatoes year-round, particularly in winter, when there is a premium for fresh, local produce. The greenhouse was in place already, but they added a water-based electric root-zone heating system complete with bottom and side insulation. Their calculations proved to be correct, in that it took approximately two years to gain their return on investment. That calculation also included the cost of the greenhouse. They sold their product for premium prices through farmers markets and through a local grocery store. For more information and the calculation suggestions, see the SARE report Assessment of the Economic Viability of High-Value Greenhouse Production in the Further Resources section.
The greenhouse vegetable business is competitive, especially if you intend to sell through wholesale market channels. Competition from exporting countries such as Mexico and Canada has decreased the wholesale price for greenhouse vegetables. Wholesale markets for off-season produce often become saturated, and this causes produce prices to drop. Competition stems from an established domestic industry, as well as Dutch imports.
With the high costs of greenhouse production, most growers focus on high-value crops. Tomatoes are the leading greenhouse vegetable crop, followed by European cucumbers, herbs, lettuce, peppers, and strawberries. The leading states in organic greenhouse vegetable production are Alaska and Connecticut. For general greenhouse crop production, California and Texas lead in production (USDA NASS, 2019). This is where the centers of production exist, both as a source of competition and as a source of supplies and technical assistance.
Greenhouse Costs
Every operator will have different costs associated with their greenhouse, so it is important to understand what your costs are. The same goes for income generated from your greenhouse. Prior to sinking lots of money into a greenhouse venture, growers should examine produce prices in their region and estimate their cost of production, including the cost to build a greenhouse. There are many calculators to help you examine different greenhouse enterprises.
Greenhouse Budget Calculators
An interactive greenhouse budget calculator is available for up to five different crops. The Interactive Greenhouse Crop Budget was designed by Dr. Robin G. Brumfield, Specialist in Farm Management, Rutgers, The State University of New Jersey at New Brunswick (2018). Dr. Brumfield has also developed a Greenhouse Cost Accounting program to help greenhouse growers understand costs for specific crops.
Another free virtual greenhouse calculator, called Virtual Grower, will give you annual costs of heating, cooling, and lighting for specific locations and is available at no cost from the USDA Agriculture Research Service. It allows for inputs such as greenhouse materials, location, type of plants grown, amount of lighting, and size of greenhouse. This can give you an accurate idea of your costs as you get started with an operation, until you are able to understand your own costs through recordkeeping. As an example, this tool calculates the annual heating, cooling, and lighting costs for a greenhouse in Pueblo, Colorado, to be around $12,000 for a 100-foot by 30-foot polycarbonate paneled greenhouse with double poly on the top. To input your own data points, see the virtual greenhouse calculator and guidance.
Keep in mind that these calculations are for conventional greenhouse systems. The fertilizer, pest management, and labor costs may increase for organic production systems.
A study on organic greenhouse strawberry production in Florida indicated that organic strawberry return on investment was greater than the return on conventional greenhouse-grown strawberries. Both conventional and organic greenhouse strawberries yielded a significantly higher return on investment than field-grown strawberries. The authors noted that although greenhouse production requires a significantly larger capital investment, the potential profits of greenhouse-grown organic strawberries were as much as 9.5 times greater than field production (Cantliffe et al., 2008).
Table 4. Strawberry Production Costs and Return per Acre | ||
Type of Production | Costs per Acre | Profits per Acre |
Organic greenhouse | $158,076/acre | $25,602/acre |
Non-organic greenhouse | $168,951/acre | $3,855/acre |
Field grown | $25,602/acre | $2,419/acre |
Source: Cantliffe, et al., 2008 |
The new publication from the Growing for Market editor, Andrew Mefferd, titled The Organic Greenhouse and Hoophouse Grower’s Handbook, suggests that there are certain costs for which it pays to spend more. One of those products is seed. Seed for greenhouse varieties is typically priced higher than seed for field-grown varieties. Maine-based Johnny’s Selected Seeds suggests that you get what you pay for when selecting specialty varieties for greenhouse production. The breeding and development of protected-culture varieties is much more specialized, and the return should be greater to justify the extra investment required by the breeder, as well as the grower (Johnny’s Selected Seeds, 2013).
Greenhouse Revenues
Greenhouse vegetable yields, along with marketing channel, determine potential gross sales. Typical yields of greenhouse tomatoes are 20 to 30 pounds per vine, or two to three pounds per square foot. Greenhouse cucumbers yield around two dozen fruits per vine. Greenhouse peppers yield two and a half to three pounds per square foot. A study conducted on supplemental LED lighting in tomatoes demonstrated a 40% increase in yield compared to the control. This was a meta analysis of numerous studies, so they did not look at whether the costs of LED lighting systems justified the yield increase (Appolloni et al., 2021). If you are trying to grow fruiting crops in the winter in northern latitudes, these will require supplemental lighting. This is an important cost calculation because the lighting costs will be significant and subject to variations in electricity costs.
In greenhouse tomato production, for example, increasing the yield from 20 to 25 pounds per plant would increase revenue by $3,960. A yield increase of five pounds would principally increase harvest, packing, and marketing costs by $1,162, leaving an additional return to labor and management of $2,798. Yield increases of this magnitude could happen through variety adjustment, fertility adjustment, pollination, and pest management. These yield estimates are probably unrealistic for a beginning greenhouse grower, however, and realistic yield estimates for beginning growers should be accounted for when starting a greenhouse business. It is more likely that inexperienced greenhouse growers would have a yield closer to 15 pounds per vine (Hochmuth et al., 2001).
The Texas A&M Small Acreage Horticulture Guide estimates that for a year-round greenhouse facility growing cucumbers, lettuce, and tomatoes with an evaporative cooling system, costs are $7 to $10 per square foot and $20 to $25 (more for hydroponic operations) on the higher end. With yield potentials of between one and 25 pounds per square foot, the profit potential can be up to $20 per square foot, once your return on investment has been made from the actual building of the greenhouse. When estimating profit, especially for a beginning grower, go for the middle of this figure (Texas A&M AgriLife Extension, no date).
As a suggestion, growers should gather all the economic data they can about the greenhouse vegetable business before building a greenhouse and understand how much the greenhouse will cost per square foot before deciding what to grow in it. Revenue is going to depend on your location and marketing channel. We suggest exploring other greenhouse business enterprises and determining whether vegetables provide the best return on investment. As an example, greenhouse vegetable growers in some parts of the country have begun to diversify into spring bedding plants because that market is more lucrative.
Developments in the Greenhouse Industry
One exciting development is the introduction of bumble bees for greenhouse tomato pollination. Pollinating by hand is expensive (in terms of labor), tedious, and time-consuming. Several companies are now raising bumble bees to be used for indoor pollination. Although the hives are expensive, they pay for themselves many times over.
There have also been many new biological-based pesticides in the last five years. Some of these biorational pesticides (also known as least-toxic, environmentally friendly, or biopesticides) include Bacillus thuriengensis (for brassica pests) and Beauveria bassiana. Use of biological control agents has also increased in the last decade. Much more is known about how to use these insects to their fullest advantage and about how to apply insecticides while preserving predators. For more information on these, see ATTRA’s Sustainable Pest and Weed Control Database.
Another change that is occurring is in the field of greenhouse coverings. Modern greenhouse plastics are resistant to breakdown from ultraviolet light and are rated to last several years. This reduces annual expenses for materials, labor to reglaze, and fees for landfill disposal. Structured sheets are the deluxe alternative to Quonset-style plastic houses. They are more expensive to purchase and install, but they provide optimum environmental controls and have a very long life. Research into the chemistry associated with greenhouse glazing is aimed at energy savings, pest control, and enhancement of plant growth.
Conclusion
Organic greenhouse vegetable production has potential as a niche market for out-of-season produce and as a sustainable method of production. Soil-based systems are readily adaptable to certified organic production, but special care must be taken for soil-borne disease control. Soilless systems can also be adapted to organic production; however, the certification of these systems can be more difficult. Organic greenhouses require a steep initial investment. Cost-of-production calculations are important to understand. Finding a suitable market and selling into lucrative markets will help earn back your investment.
References
Adams, 2017. Paul. What will it really take for vertical farms to succeed? The Counter.
Appolloni, E., F. Orsini, G. Pennisi, X. Gabarrell Durany, I. Paucek, and G. Gianquinto. 2021. Supplemental LED Lighting Effectively Enhances the Yield and Quality of Greenhouse Truss Tomato Production: Results of a Meta-Analysis. Frontiers in Plant Science. Vol. 29, No. 12. p. 596927.
Bartok, John Jr. 2022. Email correspondence with author. November.
Bartok, John Jr. 2015. Geothermal Heat for Greenhouses. E-Extension. November.
Bartok, John. W. 2015. Natural Ventilation Guidelines. Greenhouse Management. August.
Belmontes, Alfredo Diaz. 2016. Mexican: Annual increase of 1,200 hectare for greenhouse industry. HortiDaily News. April.
Bomford, Michael. 2010. Solar Greenhouses, Chinese-style. Energy Farms.
Burfield, Tom. 2019. Mexican Greenhouse Production Soars. The Packer. August 2019.
Brumfield, Robin. 2018. Interactive Greenhouse Crop Budget. Rutgers: The State University of New Jersey at New Brunswick.
Cantliffe, Daniel, James Webb, and John Vansickle. 2008. Potential Profits from Greenhouse-grown Organic Strawberries Are Greater than Conventional Greenhouse or Field-grown Strawberries in Florida. Proceedings of the Florida State Horticultural Society. Vol. 121. p. 208–213.
Cox, Douglas. 2014. Organic Fertilizers – Thoughts on Using Liquid Organic Fertilizers for Greenhouse Plants. Stockbridge School of Agriculture. University of Massachusetts, Amherst.
Fennimore, Steve. April 2018. Soil Solarization. UC Davis Plant Science. Poster Project.
Gagne, Charles, Masaki Kurosaki, Dylan Kovach, and Neil Mattson. 2020. Guide to Grafting Tomatoes: Cornell’s Tips for Success. Controlled Environment Agriculture Program. Cornell University. October.
Gougoulias, Nikolaos. 2011. Assessment of a Fertilization Management Program- Soil Salinity in Greenhouse Cucumber Crops. University of Craiova. Vol. XVI (LII). Department of Plant Production, Technological Educational Institution of Larissa, Greece.
Grubinger, Vern. 2010. Organic Greenhouse Tomato Nutrition. University of Vermont Extension.
Hochmuth, G.J., W.D. Thomas, M.S. Sweat, and R.C. Hochmuth. 2001 (Updated 2008). Financial Considerations – Florida Greenhouse Vegetable Production Handbook, Vol 1. University of Florida- IFAS Extension.
Johnny’s Selected Seeds. 2013. Protected Culture Growing Basics.
Liang, Y., X. Lin, S. Yamada, M. Inoue and K. Inosako. 2013. Soil degradation and prevention in greenhouse production. Springer Plus, December 11. Vol. 2, Suppl 1. p. S10.
Liu, X., Z. Li, L. Zhang, Y. Liu, Y. Li, and T. Li. 2021. Effect of single tube sections on the structural safety of Chinese solar greenhouse skeletons. Scientific Reports. Vol. 11. p. 19307.
Lounsbury, N., S. Birthisel, J. Lilley, and R. Maher. 2022. Tarping in the Northeast: A Guide for Small Farms. University of Maine Extension. Bulletin #1075.
Maluin, F.N., M.Z. Hussein, N.N.L. Nik Ibrahim, A. Wayayok, and N.Hashim. 2021. Some Emerging Opportunities of Nanotechnology Development for Soilless and Microgreen Farming. Agronomy. Vol. 11, No. 6. p. 1213.
Mefferd, Andrew. 2017. Greenhouse and Hoophouse Grower’s Handbook. Chelsea Green Publishing, White River Junction, Vermont.
Miles, Carol, Jonathan Roozen, Elizabeth Maynard, and Timothy Coolong. 2015. Fertigation in Organic Vegetable Production Systems. E-Extension.
Miles, Carol, Lisa DeVetter, Shuresh Ghimire, and Douglas G. Hayes. 2017. Suitability of Biodegradable Plastic Mulches for Organic and Sustainable Agricultural Production Systems. HortScience. Vol. 52, No. 1. p. 10-15.
Miller, Sally. 2018. Managing Diseases of Organic Tomatoes in Greenhouses and High Tunnels. The Ohio State University. E-Organic.
Morgan, Lynette. 2021. Organic Soilless Greenhouse Systems, Chapter 7. In: Hydroponics and Protected Cultivation – A Practical Guide. CAB International, Oxfordshire UK. p. 100-114.
National Agricultural Law Center. 2020. The Fight for Organic: Hydroponic Certification Under Fire. November.
National Organic Standards Board. 2010. Production Standards for Terrestrial Plants in Containers and Enclosures. Formal Recommendation by the National Organic Standards Board (NOSB) to the National Organic Program (NOP). April.
Perkus, E., A. Pfeiffer, C. Thurston, L. Fucui, and J. Grossman. 2019. Options for Including Cover Crops in High Tunnel Rotations in the Northern United States. E-Organic.
Sanford, Scott. 2011a. Greenhouse Unit Heaters: Types, Placement, and Efficiency. Publication A3907-02. University of Wisconsin Cooperative Extension. University of Wisconsin, Madison, WI.
Sanford, Scott. 2011b. Using Curtains to Reduce Greenhouse Heating and Cooling Costs. Publication A3907-03. University of Wisconsin Cooperative Extension. University of Wisconsin, Madison, WI.
Sutterlin, William, R., PhD. 2011. Phase Change Materials, A Brief Comparison of Ice Packs, Salts, Paraffins, and Vegetable-derived Phase Change Materials.
Texas A&M Agrilife Extension. No date. Greenhouse Vegetables Crop Guide. Texas A&M Small Acreage Program.
Thomas, Andrew, L. A. Becker, and R.J. Crawford Jr. 2003. An Energy-Efficient Solar-Heated Greenhouse Produces Cool-Season Vegetables all Winter Long. Community Food Systems and Sustainable Agriculture. University of Missouri. Columbia, MO.
Tuzel, Y., Hale Duyar, Golgen Bahar Oztekin, and Özlem Gürbüz Kılıç. 2013. Effects of winter green manuring on organic cucumber production in unheated greenhouse conditions. Turkish Journal of Agriculture and Forestry. Vol. 37, No. 3. p. 315-325.
United States Energy Information Administration (USEIA). 2021. Biomass Explained: Biomass and the Environment.
University of Georgia Extension. 2014. Greenhouses: Heating, Cooling and Ventilation. Bulletin 792. UGA Cooperative Extension.
USDA Agricultural Marketing Service (AMS). No date. Allowed Mulches on Organic Farms and the Future of Biodegradable Mulch.
USDA Agriculture Marketing Service (AMS) National Organic Program. 2021. The Program Handbook: Guidance and Instructions for Accredited Certifying Agents and Certified Operations.
USDA Economic Research Service (ERS). 2019. 2019 Organic Survey. Volume 3, Part 4 AC-17-SS-4. Table 14, p. 128.
USDA NASS. 2019. Census of Horticulture. United States Department of Agriculture/National Agriculture Statistics Service, Washington, DC.
USDA National Organic Program. 2018. Status of Organic Hydroponics, Aquaponics, and Aeroponic Production Systems. National Organic Standards Board Fall 2017 Updates. Organic Insider. January.
Western Sustainable Agriculture Research and Education (SARE). 2011. Solar Energy for Sustainable Year Round Production. Final Report for FW05-011. Don Bustos. Santa Cruz Farm.
Further Resources
General Greenhouse Information
The Greenhouse and Hoophouse Grower’s Handbook. 2017. By Andrew Mefferd. Chelsea Green Publishing.
A comprehensive guide to organic vegetable production using protected culture including structure information, best practices for the eight most profitable crops, and economic and marketing information.
Marketing
Intermediated Marketing Tutorial. National Center for Appropriate Technology ATTRA Sustainable Agriculture Program.
A tutorial that outlines considerations and tips for selling to restaurants, independent groceries, institutions, and aggregators.
Greenhouse Energy Considerations
Agricultural Ventilation Fan Performance Test. No date. By University of Illinois Department of Agricultural and Biological Engineering.
The University of Illinois, Department of Agricultural and Biological Engineering maintains this database of performance tests on agricultural ventilation fans. The performance test results, and efficiency ratings can be used to select ventilation fans based on energy use.
Cold-Climate Greenhouse Resource: A guidebook for designing and building a cold-climate greenhouse. 2013. By Jody Rader, Dan Handeen, and Virajita Singh. The Regents of the University of Minnesota. Minneapolis, Minnesota.
This manual takes a comprehensive look at the motivations to grow vegetables year-round in a cold climate, as well as design considerations and building components for a year-round, low-energy-input greenhouse.
Deep Winter Greenhouses. No date. By University of Minnesota Extension.
This page offers passive solar greenhouse designs for winter vegetable production. Included is a link to research-based design specifications for a farm-scale solar greenhouse.
Fuels and Alternate Heat Sources for Commercial Greenhouses. 2013. By John Bartok Jr. Center for Agriculture, Food, and the Environment at UMass Amherst.
This article gives a good overview and cost comparison of the most common fuels used to heat greenhouses and of some alternative fuels.
Geothermal Greenhouses: Exploring the Potential. 2021. By Victorian Smart, Danielle Miska, and Katie Simpson-Johnson. National Center for Appropriate Technology ATTRA Sustainable Agriculture Program.
This publication provides basic information on geothermal energy technology and its potential in greenhouses.
Geothermal Heat for Greenhouses. Extension.org.
Geothermal greenhouse resources.
Greenhouse Energy Conservation Checklist. 2019. By John Bartok Jr.
This paper is a quick reference list of the most cost-effective energy-saving measures that can be incorporated into greenhouse design and management. It can be found as a post on NCAT’s Agrisolar Clearinghouse website.
Greenhouse Energy Self Assessment. No date. By USDA NRCS. University of Wisconsin.
This is a tool developed by the Natural Resource Conservation Service (NRCS) and housed on a University of Wisconsin-hosted website. Users can enter location information and specifics about their greenhouse to learn how alternative heating, cooling, and control systems could lower energy usage and related expenses.
Introduction to Greenhouse Efficiency and Energy Conservation. No date. By John Bartok Jr., and Vern Grubinger. E- Extension- Farm Energy.
This is the main greenhouse energy page on the Farm Energy Extension site. This page contains lists of gathered resources, arranged by greenhouse efficiency topic.
PSU Climate Battery Study 2018-2019 Summary. Threefold Farms.
Threefold Farm is an orchard in south central Pennsylvania. This page on the farm’s website highlights the design and installation of a climate battery heating system for a high tunnel used to grow figs. Included on the page are the results of a research project studying the performance of the climate battery at Threefold Farm that was performed by Pennsylvania State University (PSU).
Reducing New England High Tunnel Heating Costs and Fossil Fuel Usage Utilizing an Earth Air Heat Exchanger. 2023. SARE Project Report.
This is the final report on the climate battery system project at Hip Peas Farm, featured in the case study above.
Virtual Grower. No date. USDA ARS.
Virtual Grower is a decision support tool for greenhouse growers. Users can build a greenhouse with a variety of materials for roofs and sidewalls, design the greenhouse style, schedule temperature set points throughout the year, and predict heating costs and plant growth for over 785 sites within the United States. Users download and run this program on their computers, but the web version is in the beta stage. Technical assistance supporting the software can be obtained through the email contact virtualgrower@usda.gov.
Greenhouse Organic Certification
Introduction to Organic Practices Fact Sheet. 2015. By USDA Agricultural Marketing Service.
A two-page summary of the principles and requirements of becoming certified organic.
National Organic Program Handbook: Guidance and Instructions for Accredited Certifying Agents and Certified Operations. Updated regularly. USDA Agricultural Marketing Service.
This link is to the table of contents for guidance on becoming certified organic.
Soil and Fertility
Floricast: Understanding compost, vermicomposts, and teas. No date. By Neil Mattson. Cornell University Integrative Plant Sciences Program.
A seven-minute video that introduces considerations for using compost, vermicompost, compost teas, and extracts.
Organic Fertilizer and Cover Crop Calculator: Estimating Plant-available Nitrogen Release from Cover Crops. No date. Oregon State University.
A calculator that helps growers understand the cost of organic fertilizers for greenhouse use.
Options for Including Cover Crops in High Tunnel Rotations in the Northern United States. 2018. By Elizabeth Perkus, et al. E-Organic and the University of Minnesota.
This article explains how cover crops can help address problems that affect high tunnel production, such as soil-borne diseases, loss of organic matter, weed growth, and salinity build-up.
Potting Mixes for Certified Organic Production. 2018. By George Kuepper; updated by Luke Freeman. National Center for Appropriate Technology ATTRA Sustainable Agriculture Program.
Provides a summary of media and fertilizers that can be used in organic production systems.
Unusual Cover Crops in the Greenhouse. By Living Web Farms Greenhouse Soil Videos.
A six-minute video explains how Living Web Farms uses unusual cover crops to break up hard pan soil and bring up nutrients from deep in the soil.
Pest Management
Allowed Mulches on Organic Farms and the Future of Biodegradable Mulch. No date. By USDA Agriculture Marketing Service, National Organic Program.
USDA Agricultural Marketing Service answers frequently asked questions about currently allowed mulches on organic farms and the potential of using biodegradable mulches in the future.
Ecological Pest Management Tutorial. 2015. By National Center for Appropriate Technology ATTRA Sustainable Agriculture Program.
The five lessons in this tutorial provide information on what ecological pest management is, how to get started, how to implement preventive strategies, how to utilize biological controls, and how to use NCAT and ATTRA resources.
A Guide to Grafting Tomatoes: Cornell’s Tips for Success. 2020. By Charles Gagne, Masaki Kurosaki, Dylan Kovach and Neil Mattson. Greenhouse Product News. October.
Useful tips on grafting tomatoes.
How to Graft Tomatoes: An Instructional Video and Factsheet. 2013. By Judson Reid, Cornell University Vegetable Program.
Grafting can significantly increase tomato yields and increase plant resistance to soil-borne diseases – especially in greenhouse production systems. Judson Reid, Extension Vegetable Specialist with the Cornell Vegetable Program, has developed a step-by-step tutorial for growers on how to graft tomatoes.
CAFF’s On-Farm Occultation Research Report. 2018. By California Alliance of Family Farmers. Western SARE Research Report.
A report on the farmer benefit, tradeoffs, and recommendations for occultation weed management strategy.
Soil Solarization and Biosolarization. 2022. By Martin Guerena. National Center for Appropriate Technology ATTRA Sustainable Agriculture Program.
A tipsheet on how to utilize solarization to manage weeds and pests in the soil.
Soil Steaming for Pathogen, Pest, and Weed Control in High Tunnels. 2022. By Andy Pressman and Chris Lent. National Center for Appropriate Technology ATTRA Sustainable Agriculture Program.
A blog that features a case study with Bruce and Jeeny Wooster of Picadilly Farm in New Hampshire. They talk about the soil steaming method of pest control they use in their high tunnels.
Sustainable Pest and Weed Control Database. 2023. By National Center for Appropriate Technology ATTRA Sustainable Agriculture Program.
A user-friendly tool for farmers looking for pest control options that are generally softer on the environment and beneficials.
Economics of Greenhouse Production
Assessment of the Economic Viability of High-Value Greenhouse Production. 2011. SARE Project Final Report FW11-043.
This is the final report on a project that utilized a thermal-heated and cooled greenhouse to grow cherry tomatoes in the off season, as a high-value crop, and analyzed whether the return was worth the investment.
Greenhouse Vegetable Crop Guide. No date. Texas A&M Small Acreage Horticulture Guide.
Provides a very simple economic analysis of greenhouse vegetables.
Organic Greenhouse Vegetable Production
By Lane Greer and Steve Diver, NCAT Agriculture Specialists
Published January 2000; Updated June 2023 by
Tammy Howard and Chris Lent with contributions from
Ann Baier, Dan Birnstihl, and Daniel Prial
© NCAT
IP078
This publication is produced by the National Center for Appropriate Technology through the ATTRA Sustainable Agriculture program, under a cooperative agreement with USDA Rural Development. ATTRA.NCAT.ORG.